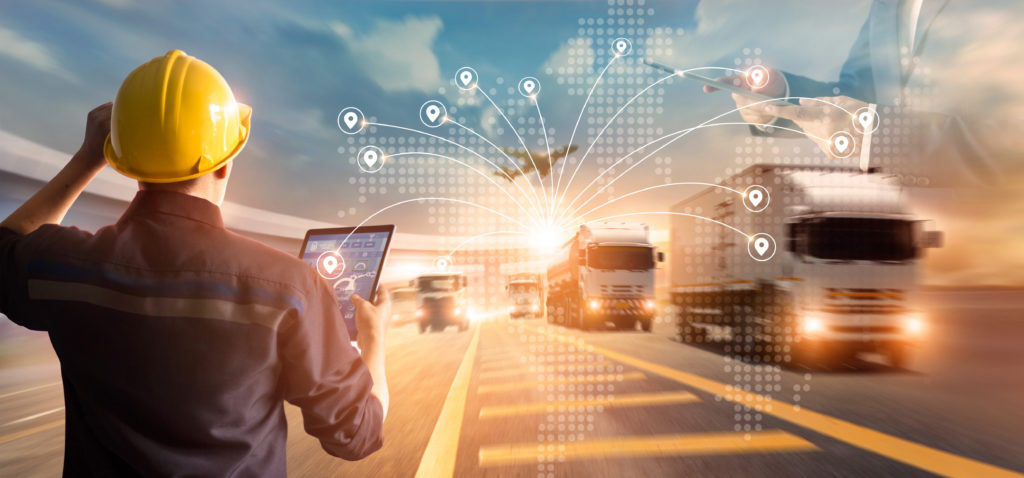
It is not news to anyone that global supply chains have taken several knocks as a result of the pandemic. With countries going in and out of lockdowns, manufacturers around the world have struggled to keep up with demand. With multiple countries closing their borders, the transportation of materials and components became near impossible. Here in the UK, manufacturers have had the added pressure of Brexit. New tariffs, customs duties and other barriers to trade had significant implications for how manufacturers could source materials, assemble products, and reach markets. The effects on supply chain over the past 18 months has been felt across all industry sectors. Whether that is a general shortage of materials in construction (global demand for cement, timber and steel outstrips supply) or more niche shortages. The absence of microchips manufactured for cars is delaying the automotive industry. Nowadays, cars are so technologically advanced that this crisis is affecting almost every car brand. Volkswagen, Tesla and Renault are among the many well-known names who have issued statements surrounding their supply chain struggles. In wake of the issues facing supply chains worldwide, the bike brand Bianchi are investing £34 million to bring manufacturing back to Italy. CEO, Fabrizio Scalzotto, expressed that “never before has Europe faced the great opportunity to bring bicycle production and technology back home”.
So, is this the answer: bring manufacturing home?
Over the last few years there has been a shift away from local suppliers toward suppliers in the Far East where purchase prices can be cheaper. Sourcing materials and manufacturing in low cost economies appears to have the benefit of reducing business costs, however, at second glance this isn’t always the reality. In fact, quite the opposite – you could be losing money.
Even before the disruption of the global pandemic, there was a clear disadvantage to sourcing materials globally rather than locally: they would have to be transported thousands of miles. In other words, they have long lead-times attached to them. If the supplier has the product available from stock, then the transportation lead time is likely to be around 6 weeks. If you’re in need of a bespoke item you must factor in the amount of time the supplier needs in order to source materials, manufacture, package and ship. This could potentially add many more weeks to the lead time. This affects your business in that you will need enough inventory to cover these long replenishment lead times. The length of time you’ll need to hold stock jumps from a few days with a local supplier (located in the UK or Europe) to many weeks when you use a global supplier (located in the Far East). There are significant cash implications of this; holding many weeks’ worth of inventory ties up your cash in SKUs. Regardless of your business this will prove damaging – even more so if you work with perishable goods or products intended to be on trend. Consumer tastes change rapidly and your business needs to keep up with the market, overstocking runs the risk of increased obsolete stock and the need to discount it to get rid! Similarly, overstocking perishable items such as food often results in items sitting in storage past the ‘use-by’ date.
All businesses should aim to improve cash flow so you should avoid tying your cash up in inventory, and companies wishing to grow will need good cash flow most of all. Businesses that struggle don’t struggle as a result of profitability – they struggle because money is limited. Maybe it’s time you stopped chasing margins and started thinking holistically about your business’ cash and growth.
Improving your cash flow is the main benefit to using local suppliers rather than global ones. However, this benefit sits alongside others: reducing your storage costs (as you’ll be holding less stock), more accurate forecasting (so less chance of stock-outs/overstocking) and reducing your business’ carbon footprint – which is proving more and more important to consumers. On top of all of that, should we ever be unfortunate enough to have to deal with another major hit to global supply chains, your business will be in a far better position.
It seems to us there is a right answer in this age-long debate!
By Lauren Wiles, Phil Snelgrove
© 2021, Goldratt UK