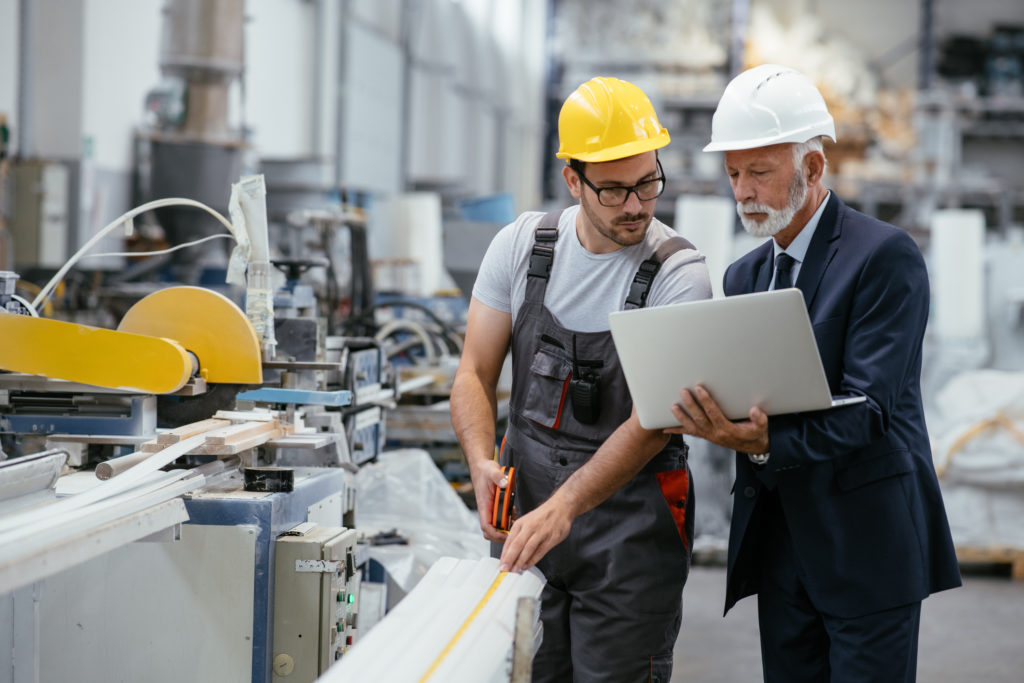
UK manufacturers seem set on accelerating the installation of automation and robotics in their production plants. As well as looking for efficiency gains, this seems to be a natural consequence of the labour shortages brought about by Brexit and various lockdowns over the last couple of years. This is driven by a strong desire to protect businesses and customers. A survey of 250 UK large and SME manufacturing companies revealed that 81.2% of companies were considering investing in robots following the pandemic[1]. This marks a distinct change in attitude for Britain. Compared to other nations, the UK has been much slower to roll out robotics in manufacturing over the years. Nigel Platt (ABB’s General Manager – Robotics and Automation UK and Ireland) attributes this in part to the UK’s ‘make-do and mend’ attitude. If you work in a manufacturing plant yourself, you will be familiar with the kudos attached to keeping aging pieces equipment operational. A machine that has been installed and kept running since the 1940s is sometimes seen as an achievement greater than making an investment in modern equipment. This has definitely been to the detriment of automation! Platt also notes further obstacles to automating UK manufacturing: fears over robots ‘stealing jobs’, a short-term vision for return on investment (ROI) and a lack of education in automation. Despite all of that, it seems the future is set – automation is the next step.
There are huge advantages to investing in robotics: higher skilled workforces, environmental benefits, increased workplace safety, better quality, higher productivity… the list goes on. However, there is one major catch – for your business to feel the benefits of automation, you must automate in the right areas. Robotics and automation could transform your business. However, it can be incredibly expensive – you don’t want to invest in the wrong areas.
Here are five things to avoid when you’re looking to invest.
1.) Don’t be in the Dark.
While an investment in automation can come with an increase in quality, repeatability and reliability, the primary aim is to increase the capacity and output that the process is capable of. If you are increasing the capacity of a particular operation (or series of operations), you need to understand the impact it will have overall on the shop floor. This boils down to two questions. Are you installing this extra capacity in a bottleneck area? Or are you installing it in a non-bottleneck area? If you don’t know, you’re in the dark and this can be dangerous.
If you don’t know, and it is a bottleneck (or a Constraint in our language) then you got lucky! Adding more capacity to an area which is capacity constrained will make your operations significantly better (provided it is managed properly). Investing in a bottleneck area will add to the capability of a process which limits your ability to produce more. Therefore, it will add to the capability of the whole organisation.
However, if automation is installed in a non-bottleneck area, then it depends on how the extra capacity is used… Having additional capacity (protective capacity) is usually a good thing, as long as it is not misused. When protective capacity is misused, Work-In-Process (WIP) increases, queues increase in front and between work centres, lead-times increase and delivery performance declines (click here for an article to explain how WIP, queues and lead-times are inextricably linked).
So, the first step towards investing in automation and robotics is don’t be in the dark. Make sure you know whether the equipment you are considering – or have already installed – is in a bottleneck or a non-bottleneck area.
Get in touch if you would like some help identifying your company’s bottlenecks.
2.) Whatever You Do – Don’t Overproduce!
Even in your bottleneck areas, the temptation will be to maximise the use of your new asset; you will be able to do bigger runs in the same periods of time – often with fewer changeovers. While this works well to achieve high efficiency and output – these jobs will be a piece of cake for your new robot – the risk is that you will be over-making. Works orders should only be for the quantities that are needed; either to put the correct inventory on the shelves or to complete the works orders to satisfy sales orders. The temptation to do large runs will decouple your customer order book (or your inventory replenishment) from the production orders you want to make on the shop floor. Every time you succumb to the temptation to run large(r) orders, you are introducing additional WIP (although efficiently made) which will contribute to further queues and choices and create extra problems.
If it’s a non-bottleneck, the same temptation will be present. This new piece of equipment is new and exciting – your engineers are going to love programming it and getting it up and running! The accountants will also have a vested interest. Your new asset has undoubtedly cost tens of thousands, hundreds of thousands, maybe even millions of pounds (depending on the level of automation); the very first thing managing directors and financial advisors will want to see is an rapid payback period and ROI. Logically, it follows that the more parts you can produce and the faster you can make them ( especially compared to previously), the quicker the ROI will improve. On the other hand, if you do not run the robot a lot it will take a long time to process many orders through it – consequently the payback period will take longer, and everyone will be looking to justify this huge expense to the company. This is completely understandable, predictable even, however, the behaviour this attitude drives is overproduction.
As we have mentioned in numerous other articles on our blog over the years, running non-bottlenecks at 100% increases WIP, extends lead-times and reduces overall output and delivery performance. So, whatever you do – don’t overproduce!
3.) Don’t Ignore Your Product Mix.
You need to pick the right automation for your mix. When considering robot automation – or new equipment of any kind – it is important to understand the additional capacity it will give you (i.e., higher rates of ouptut), but also how easy it is to switch between jobs. Changeovers, programming, tool inserts; these are all process that take time. The easier the changeover, the less time it will take and more flexible we can be. This is useful when the organisation’s product mix includes many different products, of varying quantities, for many different customers. Otherwise, the changeovers may be difficult to make but then have fast outputs once set. These are very useful when you are making similar, repeatable products time after time.
When considering robotics and automation, it is crucial to understand the business needs from the product mix and the client base you serve. It’s no good if the robot can operate at a massive run rate for a long period of time, dwarfing the output Production has achieved in the past – if you are going to have to spend eighteen out of twenty-four hours changing it over. You must also consider the time it takes to train staff to run programmes, to write them or adjust them – if these are all lengthy processes then you won’t see anywhere near the levels of output you were expecting. Don’t ignore your product mix – do pick appropriate improvements for your range and products you deliver to your customers.
4.) Don’t Get Rid of Your Old Equipment
If you are adding automation to your bottlenecks (i.e., those areas that systematically determine our ability to output jobs and deliver customer orders) then the increased capacity is going to help you. Naturally, all the new jobs will want to be routed through this new automation – the cycle times will be faster, the calculated costs lower, volumes will be higher… The consequence of that is that if you compare this to the old equipment, that equipment now appears too slow, produces lower volumes and is more “expensive” to run. It is slower. It does produce lower volumes. It’s not actually more expensive to run… but that’s a conversation for another day (get in touch if you would like to talk about product costing).
So, if that is the assumption, the temptation will be to not run any products through the old equipment – and ultimately disassemble or even sell off the slower, older machines/tooling stations/etc. This is a mistake. While the old equipment is slower, does complete lower volumes (and is maybe not more expensive!), it is also a parallel flow for constraint capacity in your organisation. This is great because while jobs can go through the automation faster, all subsequent jobs will have to queue. If you have a second, parallel work centre – even if it’s slower, even if it can only do 30% of what the new automation can – it’s an additional 30% of bottleneck capacity and allows you to run some jobs in parallel. This doesn’t make anything more expensive; ironically it speeds up the overall flow even though in isolation, the work centre is slower than the automated robotics. So, unless the previous equipment needs to be condemned, do not get rid of the old in favour of the new.
5.) Don’t Take Care of Your Bottleneck Equipment (During Production Hours!)
If you are considering automation for your bottleneck area, you must know how crucial it is to manage the capacity of that area efficiently. Adding more – and faster – capacities will be great; however, if it doesn’t solve the problem/move your bottleneck you must ensure that you are applying all the good policies that were in place with the old equipment to your new robotics. These are simple things: making sure changeovers and the running of the machine doesn’t stop when operators are taking shift changes/lunch breaks, ensuring there is always a queue of WIP in front of the bottleneck to keep the work centre running, having a quality check in place before the bottleneck to ensure that it never has to work on a defective part… The final step to maximise bottleneck capacity is to ensure that any Total Preventative Maintenance (TPM) doesn’t get in the way of production schedules and output.
There will be a whole new maintenance process to add to your environment to take care of the automation; you must still make sure that it is scheduled to be completed during times that will not interrupt production or the output of the bottleneck area. Completing maintenance at weekends for some overtime cost is often much better than losing bottleneck output. You can do the maths – how much does an hour of bottleneck downtime cost you as an organisation vs. how much does weekend TPM cost you? You might be surprised at the result.
If the automation is installed in the bottleneck area (and it should be), make sure you are applying all the rules to the new robots that you were to the equipment that was there before the robots arrived.
To learn more about the significance of your bottlenecks in your organisation our website has further resources. Also, you can follow our LinkedIn for weekly updates and more valuable content. Furthermore, you can also get in touch if you would prefer to speak to one of our experts about your system’s Constraint.
By Phil Snelgrove, Lauren Wiles
© 2022, Goldratt UK
[1] https://www.themanufacturer.com/articles/the-robotics-landscape-in-the-uk/