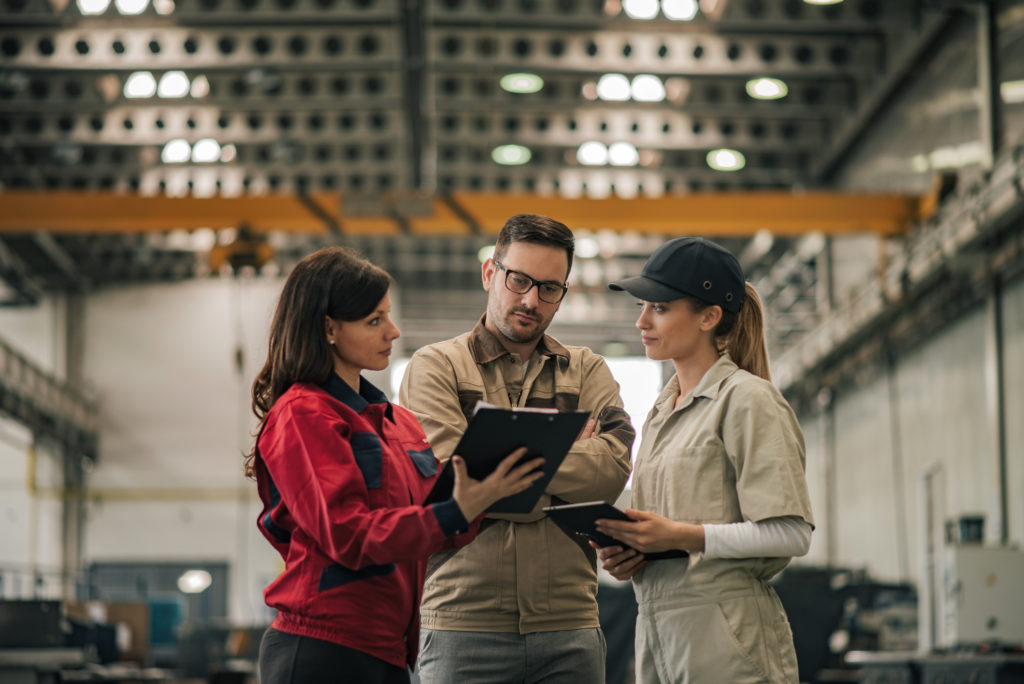
This article is the second in our four-part series detailing how to deliver on-time, every time. Click here to read a holistic article which will walk you through the 4 steps to take – in the best sequence – to achieve high OTIF (on-time in full). Click here to read the first step: ‘Release Dates are the Key to Reducing Lead-Time’.
Each article delivers value in its own right and can be read as a standalone piece.
There isn’t an organisation in the world that doesn’t try to maintain a good priority system. If your people are not clear on the priorities, business performance suffers. This makes sense; if you don’t have a good priority system then you likely have many resources spread across many departments working on different projects and tasks at different times. If this is the case, activities and ultimately customer orders don’t get completed quickly… When there are many incomplete jobs on the shop floor, the levels of Work-In-Process (WIP) increase, the lead-time extends, delivery performance is poor and ultimately, the customer – and your people – are disappointed. So, we can be sure that setting the right priorities helps us to complete orders faster and in the correct order. In this article we will use Production organisations as our example, though the principles are valid for other types of organisations as well.
If you’re honest, you will probably admit that you have two priority systems running – and getting in each other’s way. There are the priorities set around completing customer orders and stock replenishment on time, with due date and inventory availability dictating the urgency; and then there is the human priority system which allows phrases like ‘we just had this (big) customer on the phone complaining’ or ‘this customer goes golfing with the manager’ – which also can determine which task/project/order takes priority. Manually reacting to situations and adjusting the priority system causes huge disruption and often does more harm than good. You need your shop floor to be governed by a simple and robust priority system which doesn’t need to be interfered with (at all). It is also worth noting that, if you are considering improving your company’s priorities and priority adherence, this is very difficult to achieve when the levels of Work-in-Process (WIP) are high. So, before you worry about your priority system, you should consider reviewing and ensuring your release dates and lead-times are correct.
At its heart there should be two main priority drivers for production environments: there is stock (availability and replenishment) and on-time delivery. Our focus here will be on-time delivery but the principles for prioritisation will be the same regardless. (If you are running a Made-to-Stock environment, or even more challenging – a mixed environment with Make-to-Stock and Make-to-Order, and you want to talk about how you should be managing your priorities, get in touch with Goldratt UK)
So, you want your shop floor to be governed by a simple and robust, due date and lead-time driven priority system.
There are a couple of simple statements that are worth making. The first is that in a due-date driven system, where you are trying to prioritise jobs so that they finish on-time, the due-date must be the important factor in the prioritisation system. We can assume that the closer we get to the due date, when an order is not yet complete, the greater the risk that we are going to miss it. If the order is due in ten days’ time, you have plenty of time – if it’s due in half an hour, you’re in trouble! The second is the amount of lead-time that the item should be ‘live’ on the shop floor. For example, if there is one day left until the due date but the appropriate lead-time for the order is only one day, then you essentially have 100% of the lead-time left – the order should be fine. However, if you only have one day left until the due date and the appropriate lead-time for the order is ten days (much more work content), then this job should be considered ‘urgent’ – especially if you are not close to finishing the product, you will be in trouble.
Therefore, the two key factors that should drive a priority system in a Made-to-Order (MTO) environment are: the remaining time from now until the due date, and the correct amount of lead-time that the item should be ‘live’ on the shop floor.
There is a simple mechanical process using these two factors which can drive the right priorities. It is to take appropriately sized lead-times and divide them into a simple red, amber, and green priority system. As an order approaches its due date it becomes more urgent – we colour the order red if it is the final third of its lead-time. When a works order is halfway through its lead-time, it needs monitoring to ensure it doesn’t get in trouble – we colour any job in the middle third of its lead-time amber. Finally, for a job that has just been launched (i.e., in the first third of its lead-time), we colour it green. This means that all works orders, regardless of whether their lead-time is three days or thirty days, have a red, amber, or green priority indicator based on how much of the lead-time has been consumed. For example, an order with a three-day lead-time would turn red on day three; an order with a thirty-day lead-time would turn red on day twenty-one. Providing these simple colours visible to operators, managers, support staff, suppliers, etc. allows everybody to have a clear understanding of what the most important job on the shop floor is. This will be the one closest to its due date. Following this priority system will drive high on-time completion behaviours as you would be ensuring no job is left to the side as its due date approaches.
It’s relatively easy to apply these criteria to the status of works orders as most ERP/MRP systems have lead-time, due date and today’s date information recorded. We would also advocate the value of physically colouring the WIP in production with the appropriate colours so that anyone on the shop floor can see the most important order among a group of orders at a glance. In recent history, the best and most accurate way for us to communicate these priorities to all staff members is to put up screens in all departments – this has become much easier with advancements in technology and reduction in costs.
Having good priorities is one thing, following them is another! If you go into an organisation with two priority systems; the date driven system and the informal ‘which customer screams louder’ priority system – then just having colours doesn’t meant they will be followed. So, how do we get people to follow it? On the shop floor the rules are easy. Reds take priority over ambers; ambers take priority over greens – and you shouldn’t be launching orders too early. If you have two jobs of equal priority (i.e., same colour) you can leave the order to shop floor intuition. Operators can make good decisions on how to optimise output – but only within the same colour group. If you can convince your workers that going to stick to the priorities and management is not going to violate them, then you will see very quick adoption on the shop floor. A simple priority system which brings stability and predictability as there is no chopping and changing tasks, so this is typically sufficient provided management and other departments don’t try and violate the system. The harder part of enforcing the new priority system is making sure management – or other outside influences – refrain from interfering with the priority setting.
When the WIP on the shop floor is visually coloured red, then amber, then green so that everybody can see it – and when operators are asked to execute in the order red, then amber, then green… then very quickly there is an increase in control on the shop floor, and an increase in flow and output. To support this, you need your reporting system to have information in line with the priority criteria – it needs to be able to show you the reds, ambers, and greens, and it needs to know where the WIP is located so that management can see the colours in different departments. You need this data visible and up to date.
You can upgrade your existing systems to be able to report on this information. It can show you the colours and tell you how much of the lead-time has elapsed relative to the due date. It can also show when the work has moved from one machine/department to another so that you know where the WIP is. If you have that information, you can provide machines/departments/supervisors with up-to-date lists of orders and in the sequence of the priorities.
A good system should:
- Be able to store lead-time information.
- Be able to be modified to apply the red, amber and green status (in thirds of lead-time) for all orders.
- Be able to record and report on where the WIP is currently located – based on bookings and routings.
- Be able to produce customised reports for each machine, each department, and for each supervisor to show what’s queuing and running in their department (prioritised by colours).
If your system doesn’t already have these functions, contact us for more information on Ropeweaver. Ropeweaver is a tool designed to support companies’ native ERP/MRP systems. Click here for an article detailing the areas it can help you with or get in touch for a demonstration/more information.
To be the first to know when the next instalment of our ‘High OTIF’ series is published, you can follow our LinkedIn.
By Phil Snelgrove, Lauren Wiles
© 2022, Goldratt UK