Manufacturing organisations have always faced the same dilemma over what is the appropriate batch quantity to manufacture – whether that is a Minimum Batch Quantity (MBQ) or an Economic Batch Quantity (EBQ) or quantities that match customer orders exactly. These terminologies can be heard in planning meetings around the world… This tells us there is a big challenge around deciding how many to make and how often to make them. This is true for both companies who make to customer order, and especially for companies that make to stock. Businesses that manufacture goods to have inventory on the shelves have the added pressure of believing that they know that the components will eventually be sold and used, so they are planning to live with a level of inventory in stock. This means large(er) batch sizes through Production are a fact of life.
So, if many people from all over the world keep working on this question, why haven’t we settled on an answer?
The dilemma hasn’t been solved yet because there are two very valid needs that lead us to two conflicting policies about batch sizes. On the one hand, if you run a production facility, the more you manufacture/produce (that customers want to buy), the more money you will generate. To make more, you need high output; to have high output, you don’t want to spend your time constantly chopping and changing setups and equipment over – you would prefer to run big batches. So, from an efficiency/productivity/volume perspective, the bigger the batch you can convince the company and planners to allow you to manufacture, the higher the output you are going to have.
But then, on the flip side, every organisation that manufactures something needs to get their goods to market as quickly as possible. That’s when the business gets paid; that’s when the customer is satisfied. Nowadays with the likes of Amazon Prime and various other next day delivery options, consumers expect products almost instantly. Of course, depending on the industry, there are still companies with six-to-eight-week lead-times, but the drive is to become faster and faster. In order to be responsive to your market and win customer sales, you need to have short and fast lead-times; to ensure short, fast lead-times, you must have low queues on the shop floor; you need to run small batches which pass through production very quickly.
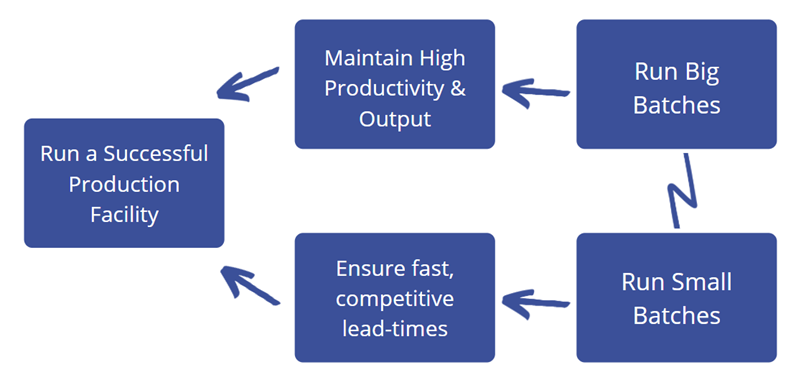
This why, still today, we have this dilemma about what is the best batch size to manufacture. There are two areas you need to focus on to have a positive impact on both the output and the lead-time requirement.
The first step is to understand that there is a difference between process batches and transfer batches. Process batches refer to the size or the quantity of works orders that we generate (i.e., the number of pieces we are asking each operation to produce). Transfer batches are the size or quantity that you move from the first process in the operation, to the second, to the third, and so on. Usually, these two batches are the same size. If you launch a batch of ten components to be manufactured at Operation 10, the operator will typically process all ten, then move all ten to the next operation. However, this is a policy – not a physical requirement. Of course, all ten parts need to me processed (a process batch of ten) but you can decide to transfer these to the next operation in batches of five, of two or even batches of just one. Yes, there might be some additional logistics involved with working out how to trace and move the material, but let’s look at the benefits.
Let’s say that you have three operations (Op 10, Op 20 and Op 30). You have a process batch of five and a transfer policy of five. To keep things easy, let’s also say that each operation takes one minute to complete, and it takes no time at all to move parts to the next operation. So, the entire process is completed within 15 minutes. You’ll notice in the diagram below, that the first part will be available to sell after minute 11.
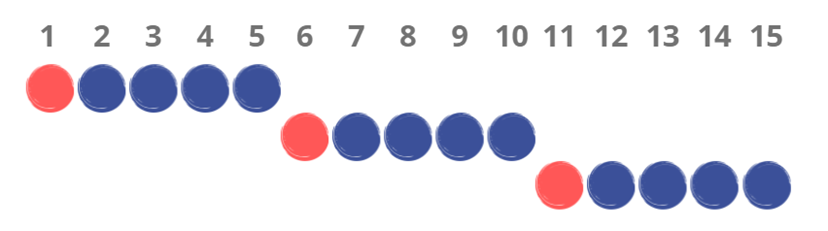
Now imagine a separate scenario. You still have a process batch of five, no work centre (Op 10, Op 20, Op 30) experiences any drop in output. There are no additional setups, they are working on the same size batches – but look at the impact on the lead-time.
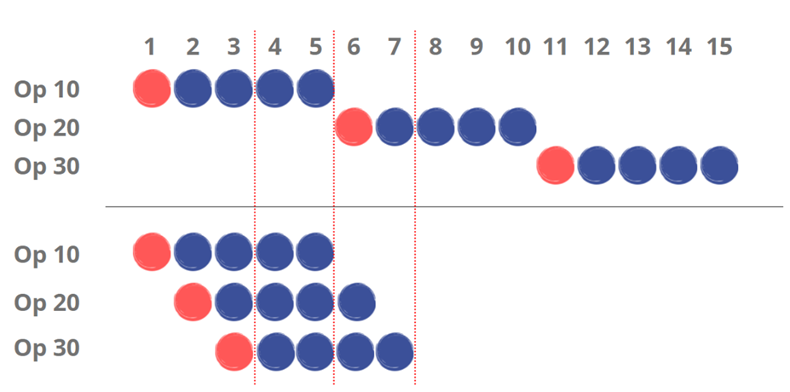
The time it takes for the whole process to be completed crashes to nearly half and the time for the first part to become available to sell improves by nearly triple. What’s more, this is only a simple example with just three operations and batches of five… imagine these improvements being made over a vast product range.
So, let’s understand why this small amendment has such a significant impact on lead-time. When you process the first unit of any batch, the remaining quantity in that batch is waiting to be processed. Then, when the first unit is completed, the second unit gets worked on – still the balance of that batch size is waiting for the second unit to be completed, and so it goes on. The same is true for a completed unit. When part number 1 has been processed by the first operation, it must wait for all the remaining parts in its batch before it is available to be moved onto the next operation. So, the bigger the batch, the majority of a part’s life is spent waiting (non-value-added time). This is true in isolation; in combination, what this looks like on the shop floor, is many pieces sitting queuing, waiting to be processed. When they have been processed, they are still queuing, waiting for the rest of the batch to be completed. Then, they are often waiting to be transported to the next operation – where they queue again.
So, whilst efficiency and output from the machines might be good (fewer setups/changeovers, focusing on running the same parts, etc.) the impact it has on lead-time is catastrophic.
Our first recommendation is that anything you can do to reduce the size of the transfer batch so it’s smaller than the size of the process batch – while still maintaining traceability and good organisation on the shop floor – is a good thing.
The second recommendation we have for you focuses on who decides what the right batch size should be. On the surface, it sounds like a planning decision; it’s planning who take sales orders and plan how many, and when these production orders should be live on the shop floor, so this makes some real sense. However, if you look from a different point of view, the decision to raise one production batch from two sales orders (i.e., to aggregate together) for example, and the decision to increase a batch quantity to an MBQ/EBQ (for efficiency) once it’s made at the planning level is rarely re-investigated or challenged. This means that if the right thing to do in production would be to split that batch, or make a lower quantity twice, it would be difficult to do and require additional approvals and paperwork, etc.
So, what is the other option? What would happen if you only raised works orders in planning for the actual quantities we needed, and never rounded up or aggregated? There would be smaller batches raised by planning, these would, in theory, be processed on the shop floor, require lots of set ups and changeovers etc and therefore you would lose the productivity gains, right?
But is that true? Are operators and operational managers unable to group orders together on the shop floor? Of course not, they do it all the time. You can have the same efficiency gains by running many small batches back-to-back (with no additional setups in between) when there are multiple (smaller) batches available on the shop floor. When batches are smaller, they will flow though operations much faster and you get the benefit of faster lead-times while maintaining high output.
So, maybe don’t jump the gun – leave the batching decisions to production!
Our recommendations then, in summary are:
- Transfer in batches smaller than the process batch to maintain high output on work centres and ensure fast flow through production, delivering faster lead-times without sacrificing output quantities.
- Don’t aggregate in the planning stage and avoid the temptation to artificially increase batch sizes with MOQs and EBQs so that production can make good grouping decisions on the shop floor. This will give you big batches when needed but again, the lead-times will shrink and your delivery performance will increase, for no loss in output.
For help synchronising your Operations and Planning departments on these rules and establishing what’s best for your environment, get in touch with Goldratt UK.
By Phil Snelgrove, Lauren Wiles.
© 2022, Goldratt UK