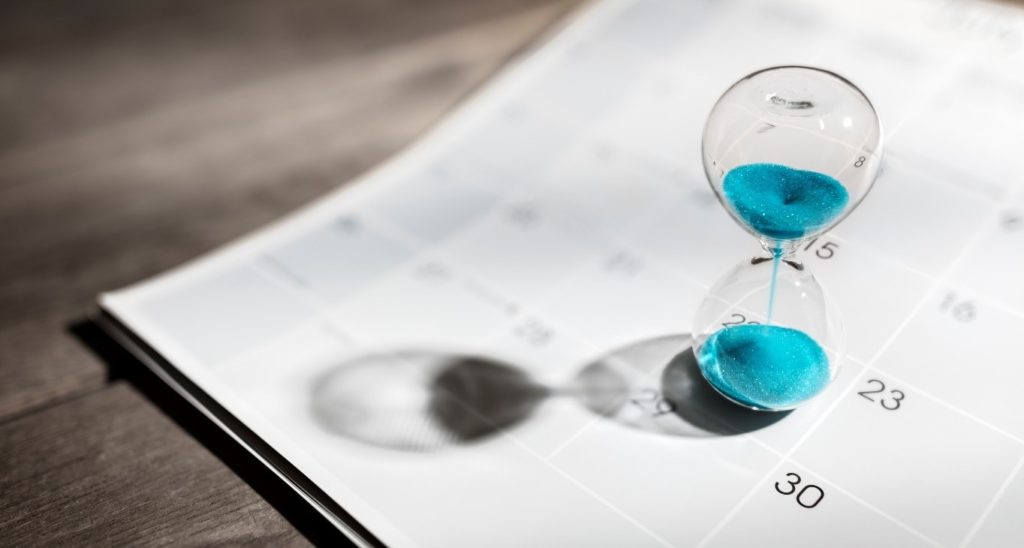
‘You don’t deliver a project one task at a time’, claimed the leader who’s project was running late, and I was trying, hopelessly, to help. That’s an interesting claim isn’t it? Don’t we build houses one brick at a time, build a car one part at time, and write articles one word at time? Why then would it be different for projects?
The management of tasks is without question one of THE primary reasons why projects deliver, or more frequently, fail to deliver on time. I learnt the importance of task management from two sources. The first was at a very small seminar with the late project guru Eli Goldratt. Goldratt, a physicist, realised that there were four task related reasons for projects running late. The second, as I’ll go on to explain, was in housing systems – not what I thought was a typical project environment.
1: The wrong task is done at the wrong time. The simplest analogy is to think about personal projects we’ve planned but failed as yet to deliver. Would it not be true that we had the time to do them but chose to do something more enjoyable or with less effort instead. Now the cleaning of the garage has been shifted till the spring… In projects it’s the same thing. Because a team has access to multiple tasks, they choose those they prefer to do or those that will be quickest. As such at the end of the week/month/quarter the difficult and longest tasks are left. Some never get done.
2: Constant shifting priorities. This is a leadership issue. Leaders fail to set clear objectives and as such constantly change their mind about what should be done. When we study a project system, we always ask the same question ‘what prioritisation rules are you working to’. The lowest number we’ve had is 12, the highest 25. What this really means of course is that there are NO prioritisation systems in the team, and team members constantly shift from working on one task to the next hour after hour.
3: Failing to unblock quickly enough. A team member sits at their desk and tries to work, but alas their task is blocked due to another team or a lack of resource etc. What are they asked to do? Stop that job and go to the next one. Imagine this scenario in a manufacturing plant? The engineer on the line tries to work on a car, there is a problem they can’t solve, they are told to remove the car from the line and go to the next one. What transpires? Lots of cars half built strewn across the factory floor. In this scenario management would get involved, wouldn’t they? They’d be horrified to see all the partly made cars all over the factory… surely? So, why not in digital manufacturing? Put simply, the part made products cannot be seen. Leaders are not close enough to the work to see that their lack of action is slowing down the work.
4: Leadership decision making. In a sense this is similar to the above issue, leaders required to make decisions on issues such as budgets or resources are not present. Tasks and deadlines slip. We conducted some research on this recently – we found on average 30% of time lost in projects is due to the failure of leaders to be present when needed.
I had gone into the seminar simply because I wanted to see Eli Goldratt, but on leaving I realised that he’d provided a huge insight into a problem I was facing. As a young consultant I was working on a job for a local authority to help them increase the speed of the turn-around of rental houses that had become empty and needed to be refurbished prior to re-letting. Suddenly the reasons for delay were clear.
1: Wrong house at the wrong time – tradesmen (they were men) were working on houses that offered the easiest jobs. If there were 100 houses to be refurbished, then they were doing a little bit of the houses at the same time. Houses with only 2-3 days of work to be done were taking months to fix.
2: Leaders were constantly changing the schedule – sometimes they’d direct the technicians to the shortest jobs (to increase their productivity numbers) sometimes they’d be sent to the ones taking the longest. Again, there were multiple priority rules. No house was ever completed, despite everyone being busy.
3: Failing to unblock – If a part wasn’t readily available the joiner would be sent to another house, now working out of sequence and when the part did become available the joiner was now busy. More delays.
4: Leadership decision making. In this system the big challenge is conflict between billing and house completion. You see these departments reclaimed money from the centre the more jobs they did, thus to claim the most money the job is keep the tradesmen busy. Only when complaints about lack of housing emerge do leaders focus on getting houses ready again. Leaders are not focused on the right issue or the purpose of the system, thus fail to make frequent or adequate decisions.
I tested Eli’s ideas in the housing system:
1: Set a strict sequence of work, do not change it. Stick to the task at hand.
2: Only allow work into the system that you want worked on, and focus on finishing that task.
3: The role of the leader is to unblock a task when it is stuck, when a job is blocked the technician stands down and waits or helps to unblock the work.
4: Plans call out when leaders will be required to make decisions on task acceleration. Late decision making is tracked and highlighted at the end of the work.
Working like this saw the team deliver more houses in record time. Years later we are still using the same principles to deliver more homes for the homeless, the numbers are staggering.
And in projects implementing these basic rules has seen late running projects, as late as 9 months over schedule, deliver earlier than their original due date. All because the team focused on the right task at the right time.
Projects are in-fact best delivered one task at time, it’s not sexy, but what other way would you possibly do it?
© 2021, Goldratt UK