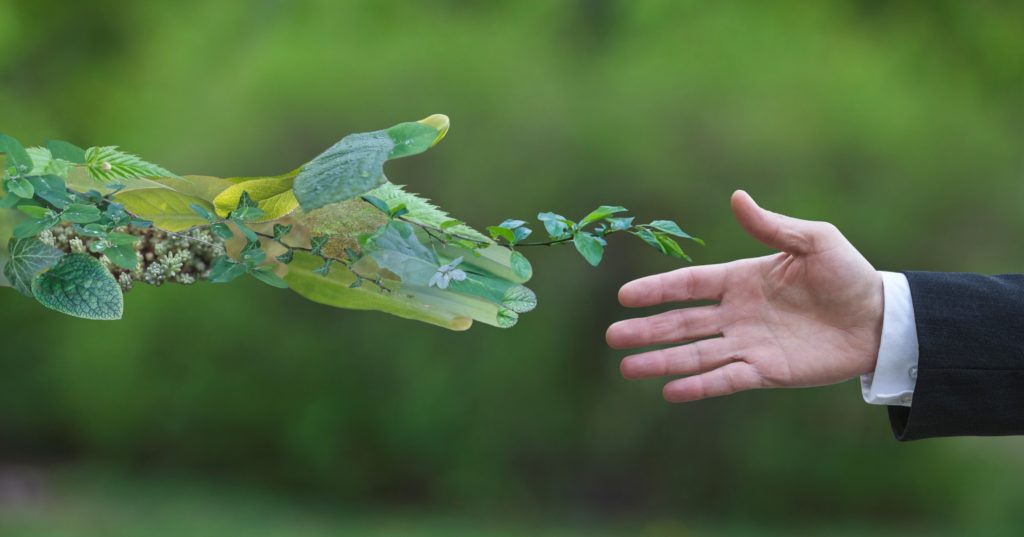
It is not new information to anyone that global warming is an incredibly important global issue. If businesses across the world continue along the same trajectory, scientists have predicted catastrophic effects at the extreme. The earth’s temperature will continue to rise. Material resources are likely to be scarce causing prices to rise as easily exploitable sources are depleted. An increase in extreme weather events may render large areas of land uninhabitable concentrating the ever-growing population and industry into condensed urban areas, less resilient to unpredictable shocks and risking supply chains. We all have a social responsibility to ensure we are living as sustainably as possible.
There are many benefits to businesses operating more sustainably. Making environmental and societal improvements goes hand-in-hand with profit making. Make UK reported that “manufacturers who put sustainability at the heart of their businesses have seen real benefits from doing so in the last 12 months with 40% reporting increased profit margins and 30% increased competitiveness as a result.” The report also stated that 90% of manufacturers are aware of the 2050 net-zero target, and that almost half were already committed to following through with concrete actions. Sustainability within business can be compared to the notion of continuous improvement, it is about constantly changing your businesses for the better. A great way to become more environmentally friendly as a business, without having to invest, is to simply reduce company waste.
So, how do you waste less?
Lean manufacturing is a well-known improvement methodology which aims to reduce waste while maximising productivity. The ‘Seven Wastes’ of Lean include: overproduction, inventory, motion, defects, overprocessing, waiting and transport. In this article we will approach two of these defined ‘wastes’ from a Theory of Constraints perspective. Our focus will be on overproduction and inventory as these two have the largest potential to significantly impact the environment.
Overproduction essentially means that you are manufacturing more of a product or service than is needed or wanted. Production requires power, capacity, heating, lighting, water – all the elements which keep the factory open. But it also consumes materials, coolants, lubricants and tooling… everything that goes into manufacturing the product. When you overproduce, this becomes waste. It is usually a cost mindset that drives businesses to promote overproduction. Naturally, you want to make the most out of what you have; the people you’ve hired, the machines you’ve purchased, the money your shareholders have invested, etc. To minimise costs, you need to utilise your capacity/resources as effectively as possible. If the priority is efficiency, you will be tempted to run big batches and large quantities through production and have fewer changeovers and setups. Chopping and changing jobs jeopardises your capacity, output, and your costs. On the other side, in order to match your capabilities to your customer orders (protect your Throughput – defined in this article) you should only make the amount that is needed. In this case, you need to allow for changeovers, or short production runs. You are only looking to produce what the customer wants at this time. This presents you with a dilemma. To make the most of what is available to you, you want to promote producing larger quantities. But that means that you are not switching to the next urgent order. This is not taking care of the customer; you are overproducing. However, if you only make what is needed for the customer, you will lose output. You will have to allow for more changeovers and lose efficiency.
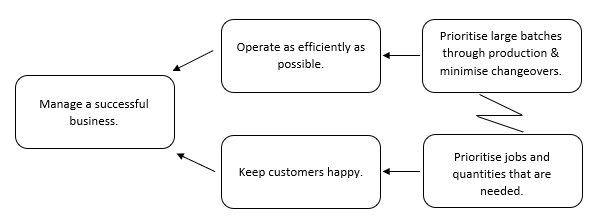
It’s difficult to manage capacity to produce enough output to keep costs under control and ensure 100% of customers are happy. This is the key to avoiding overproducing. Working on finding the balance will not only benefit your business through happy customers and efficient production but will also reduce the waste which negatively impacts the environment; it’s a win-win.
Goldratt UK help organisations manage this dilemma through finding the capacity to do both. We help find the extra capacity hidden in your organisation. So, for no extra cost, you can reduce overproduction, be more sustainable and have more satisfied customers.
The second waste, inventory, is related but not the same. When you overproduce, the number of pieces in the batch/on the palette/in the warehouse increases. This means you will have higher levels of inventory. To keep costs under control in this case, you should want to keep your inventory as low as possible. Higher inventory levels (Poorer Inventory Turns) means you must continue to warehouse it which has costs attached. So, from a cost mindset you want to keep inventory nice and low. However, the danger is that if inventory is too low, you can miss sales and customers are left unsatisfied. So, you must make sure there are always products available for customers to buy – this tempts you to maintain high inventory levels…
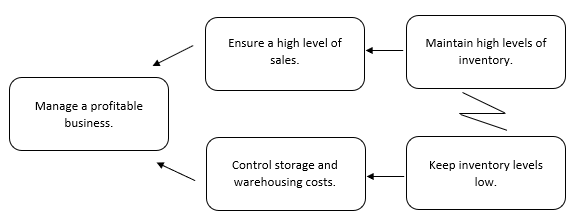
Another danger to having excess inventory is that it is potentially damaging to the environment when you consider the packaging, transportation, storage, and everything that comes along with it.
Goldratt UK works with stocking environments to reduce the levels of Purchased Goods, Work-in-Process, Raw Materials and Finished Goods Inventory without jeopardising output and sales. Get in touch if you would like to talk to us about that.
There are numerous ways businesses can be more environmentally sustainable. Replacing vehicle fleets with new electric vans and trucks for example or purchasing carbon offsets. However, you don’t need to invest money to become more sustainable. Simply reducing company waste through avoiding overproduction or not going overboard on inventory, can help to protect the environment. Prioritising the planet can have a positive impact on profit; make sure your business takes advantage of this special competitive edge.
By Lauren Wiles and Phil Snelgrove
© 2021, Goldratt UK